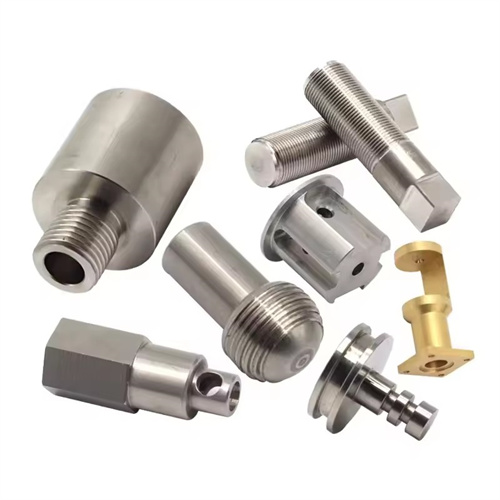
CNC Turned Components
CNC Turned Components refer to high-precision parts manufactured using Computer Numerical Control (CNC) lathes. These components are typically made from metals or plastics and feature complex geometries with tight tolerance requirements. CNC lathes rotate the workpiece and use cutting tools to remove material, producing highly accurate parts. CNC Turned Components are widely used across various industries due to their precision, consistency, and repeatability.
Manufacturing process of CNC Turned Components
Basic motion: CNC Turned Components are performed on a lathe, mainly through the rotational motion of the workpiece and the linear or curved motion of the tool.
Cutting method: The cutting energy of CNC Turned Components are mainly provided by the workpiece rather than the tool. The cutting tool performs cutting on the workpiece, thereby changing the shape and size of the workpiece.
Processing accuracy: The accuracy of CNC Turned Components can generally reach IT11-IT7, and some can even reach IT6. The surface roughness Ra can reach 12.5-0.8um, demonstrating its ability for high-precision machining.
Rough:
Rough turning is one of the main stages of turning machining. It uses a larger cutting depth and faster tool speed for preliminary processing, with the aim of quickly removing most of the rough material on the surface of CNC Turned Components. Rough cutting typically focuses on rapid material removal rather than achieving final dimensional accuracy or surface quality.
Semi polishing:
After rough turning, a semi precision turning stage is usually carried out. In this stage, the cutting depth is reduced and the tool speed is increased, with the aim of achieving the predetermined size and high smoothness of the CNC Turned Components surface. Semi precision turning is a transitional stage between rough turning and precision turning, which further reduces material removal and prepares for the subsequent precision turning.
Completing:
Precision turning is the last critical process in turning machining. At this stage, further reduce the cutting depth and tool speed to improve the dimensional accuracy and flatness of the workpiece. The main goal of precision machining is to ensure that CNC Turned Components meet the predetermined dimensional accuracy and surface smoothness requirements.
Superfinishing (optional):
For certain applications that require extremely high surface finish, the polishing stage may also be carried out. The light car adopts very small cutting depth and very slow tool speed to further improve the surface smoothness of CNC Turned Components.
Key Features of CNC Turned Components
High Precision: CNC lathes can achieve micron-level accuracy, ensuring each part meets design specifications.
Consistency: Automated production ensures uniform quality and dimensions for every part.
Complex Geometries: CNC lathes can create intricate shapes and features, such as threads, grooves, and holes.
Material Versatility: Capable of machining a wide range of materials, including metals (e.g., aluminum, copper, stainless steel) and plastics.
Efficient Production: Ideal for high-volume manufacturing, enabling quick order fulfillment.
Applications of CNC Turned Components
Below are four randomly selected industries where CNC Turned Components play a critical role:
Electronics
In the electronics industry, CNC Turned Components are used to produce connectors, pins, housings, and other precision parts for devices such as smartphones, computers, and circuit boards. The high precision and reliability of these components ensure the proper functioning of electronic devices.
Medical Devices
CNC Turned Components are essential in the medical field for manufacturing surgical instruments, implants, and diagnostic equipment. The ability to produce biocompatible materials with tight tolerances makes CNC machining ideal for meeting the stringent requirements of medical applications.
Hardware Tools
In the hardware tools industry, CNC Turned Components are used to create parts for drills, wrenches, screws, and other tools. The durability and precision of these components ensure the longevity and performance of hardware tools.
Sports Goods
CNC Turned Components are used in the production of sports equipment such as bicycle parts, golf club heads, and fitness equipment. The lightweight and high-strength properties of these components enhance the performance and durability of sports goods.
CNC Turned Components are versatile, high-precision parts that play a vital role in various industries. Their ability to meet strict tolerances, handle complex designs, and work with diverse materials makes them indispensable in modern manufacturing. Whether in electronics, medical devices, hardware tools, or sports goods, CNC Turned Components ensure superior performance and reliability.