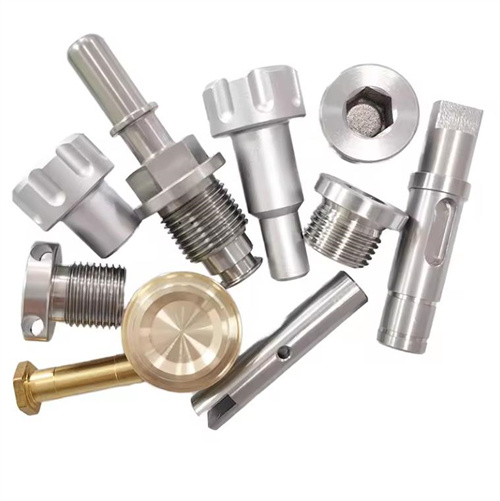
CNC Turned Parts
CNC Turned Parts are precision components manufactured using Computer Numerical Control (CNC) turning machines. These machines rotate a workpiece on a spindle while a cutting tool removes material to create the desired shape. CNC turning is highly accurate and efficient, making it ideal for producing complex geometries with tight tolerances. The process is widely used in industries that require high precision and consistency, such as automotive, aerospace, medical, and electronics.
CNC Turned Parts are typically made from materials like metals (aluminum, brass, stainless steel, titanium) and plastics. The process allows for the production of components with excellent surface finishes and intricate details. Common CNC turned parts include shafts, bushings, connectors, and fittings.
Applications of CNC Turned Parts
- Electronics
In the electronics industry, CNC Turned Parts are essential for creating precision components such as connectors, terminals, and housings. These parts are often made from conductive materials like copper or brass to ensure optimal electrical performance. The high precision of CNC turning ensures that components fit perfectly into electronic devices, enhancing their functionality and reliability.
- Medical Devices
CNC Turned Parts play a critical role in the medical industry, where precision and quality are paramount. Components such as surgical instruments, implants, and diagnostic equipment are often manufactured using CNC turning. Materials like titanium and stainless steel are commonly used due to their biocompatibility and durability. The ability to produce parts with tight tolerances ensures that medical devices operate safely and effectively.
- Hardware Tools
In the hardware tools industry, CNC Turned Parts are used to produce durable and precise components such as screws, bolts, and fasteners. These parts are often made from high-strength materials like steel or aluminum to withstand heavy use. CNC turning ensures that each component meets exact specifications, ensuring reliability and performance in various applications.
- Sports Goods
CNC Turned Parts are also used in the sports goods industry to create high-performance components for equipment such as bicycles, golf clubs, and fitness machines. For example, precision-turned parts like shafts, bearings, and connectors are critical for ensuring the smooth operation and durability of sports equipment. The use of lightweight materials like aluminum helps enhance the performance of sports goods.
CNC Turned Parts are versatile and essential components across a wide range of industries. Their precision, durability, and ability to meet tight tolerances make them indispensable in applications ranging from electronics to medical devices, hardware tools, and sports goods. As a manufacturer, producing high-quality CNC Turned Parts can help meet the demanding requirements of these industries and contribute to the development of innovative products.